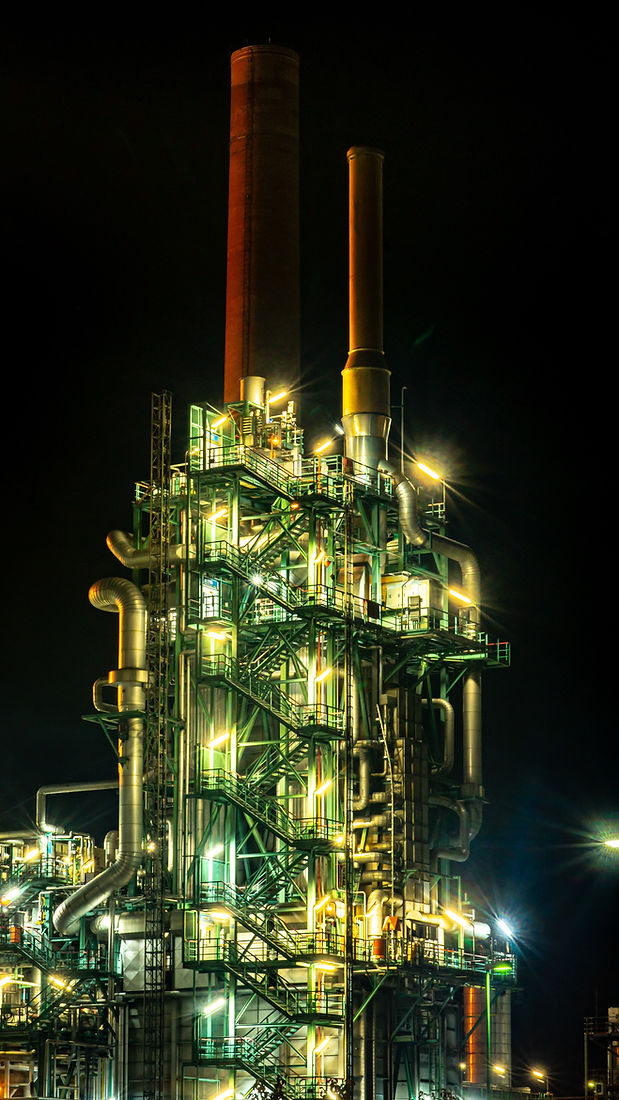
STEAM SYSTEM EVALUATION
![]() | ![]() |
---|---|
![]() | ![]() |
![]() | ![]() |
![]() | ![]() |
.png)
An expert and experienced STEAMGARD engineering team, using FLIR infrared thermal spectrography, an ultrasound recorder, and a high-temperature pyrometer conducts a thorough inspection of your steam system.
We start in the boiler room and follow all steam lines in the facility to locate steam-using equipment and evaluate how all components of the steam system work together.
Additionally, the following steam system components are evaluated:
-
piping & design
-
insulation
-
boiler setup
-
turbines
-
deaerator
-
control valves
-
check valves
-
isolation valves
-
bypass valves
-
pressure-reducing valves
-
condensate receiver tanks
-
vacuum breakers
-
air vents
-
flash tanks
-
storage tanks
-
heat exchangers
-
heat recovery stations
-
air handling units
-
coils
-
steam generators
-
dryers/rollers/ironers
-
vent-lines
-
tracers
-
process equipment
-
reboilers
-
evaporators
-
humidifiers
-
water heaters
-
autoclaves
-
sterilizers
-
unit heaters
-
cookers
-
kettles
-
dishwashers
-
cart washers
-
radiators
-
fin-tubes
-
drip legs
-
mud legs
-
condensate sample testing (upon request)
-
and various other elements are reviewed.
All the steam traps in the system are inspected/tested, photographed, and tagged.
After completing a thorough system review, we process the information gathered and prepare a comprehensive analysis, which includes primary Energy Conservation Measures (ECMs). Frequently, we suggest Secondary Energy Conservation Measures (SECM’s) for your consideration.
The STEAMGARD evaluation of the system and processes, presented in a comprehensive report, contains an analysis of cost savings and project payback expectations. The report can include suggestions for corrections or modifications to your system that can add value to or upgrade the facility’s operations. With its supporting data, photographs, calculations, charts/graphs, our report is presented to you as a working document. We review it with you and the information and your feedback becomes the blueprint for installation and retrofitting.
A representative payback calculation helps you make an informed decision about the long and short-term value of your investment.
Factors we identify in calculating the payback include:
-
Excess steam consumption caused by failed steam traps
-
Excess energy costs due to excessive steam consumption
-
Reduced maintenance costs
-
Increased process/equipment efficiency
For more information about our Steam System Evaluations or other services, please contact us at +(847)913-8400 or fill out the form below.